磁轭夹角可变的旋转磁场探伤仪

磁粉检测在锅炉、压力容器、管道等焊缝表面检测中应用十分广泛,为了提高探伤效率,检出多个方向的缺陷,经常选用旋转磁场探伤仪进行检验。但对DN300及以下的小管径对接焊缝,受旋转磁场探伤仪尺寸影响,仪器与管道表面耦合不良,检测效果较差。
为解决这一问题,设计了一种底部关节可进行一定程度活动的旋转磁场探伤仪。
01
旋转磁场的产生及分布
目前旋转磁场探伤仪大多数都使用十字交叉式磁轭及亮相电源来获得旋转磁场。如图1所示,使用三相交流电源的任意两相(A和B),调压后分开给两磁轭供电,Ua供给线圈L1和L2,Ub供给L3和L4。由于Ua同Ub之间相位差的影响,两磁轭产生的正弦交流磁场叠加,形成椭圆型旋转磁场。
图1 交叉磁轭法
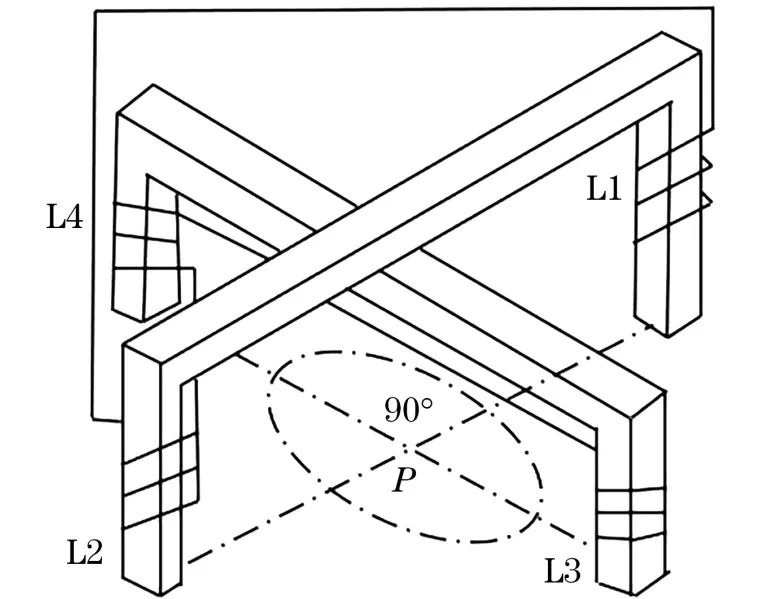
设两磁轭产生的正弦交流磁场分别为HA和HB,HA与HB夹角为θ,且两磁场幅值相等,表达式分别为公式(1)和(2),φ为两交流磁场间的相位差:
HA=Hm sinωt (1)
HB=Hm sin(ωt-φ) (2)
取ωt=θ/2,ωt=φ/2,ωt=(α+φ)/2,代入公式(1)和(2)中,得到图1中P合成磁场的轨迹方程:

由式(3)可得,旋转磁场的轨迹由磁场强度Hm、两磁场间夹角θ以及两磁场间的相位差φ共同决定。前文已假设两磁场幅值相等,当cos(θ/2)cos(φ/2)=sin(θ/2)sin(φ/2),即θ+φ=180°时,P点旋转磁场轨迹为圆,其余时刻为椭圆。
02
仿真模型的建立与研究
通过COMSOL软件建立有限元三维模型,设置相关参数并进行仿真分析。
磁轭夹角逐渐增大时,保持磁轭夹角相位差不变,P点磁场由圆形变化为椭圆形,进行参数化扫描,获得中心点P处磁场的变化轨迹。如图2所示,θ=90°时,P点磁场轨迹近似圆形,θ=60°时,P点磁场轨迹近似椭圆,与理论推算一致。
图2 P点磁场轨迹
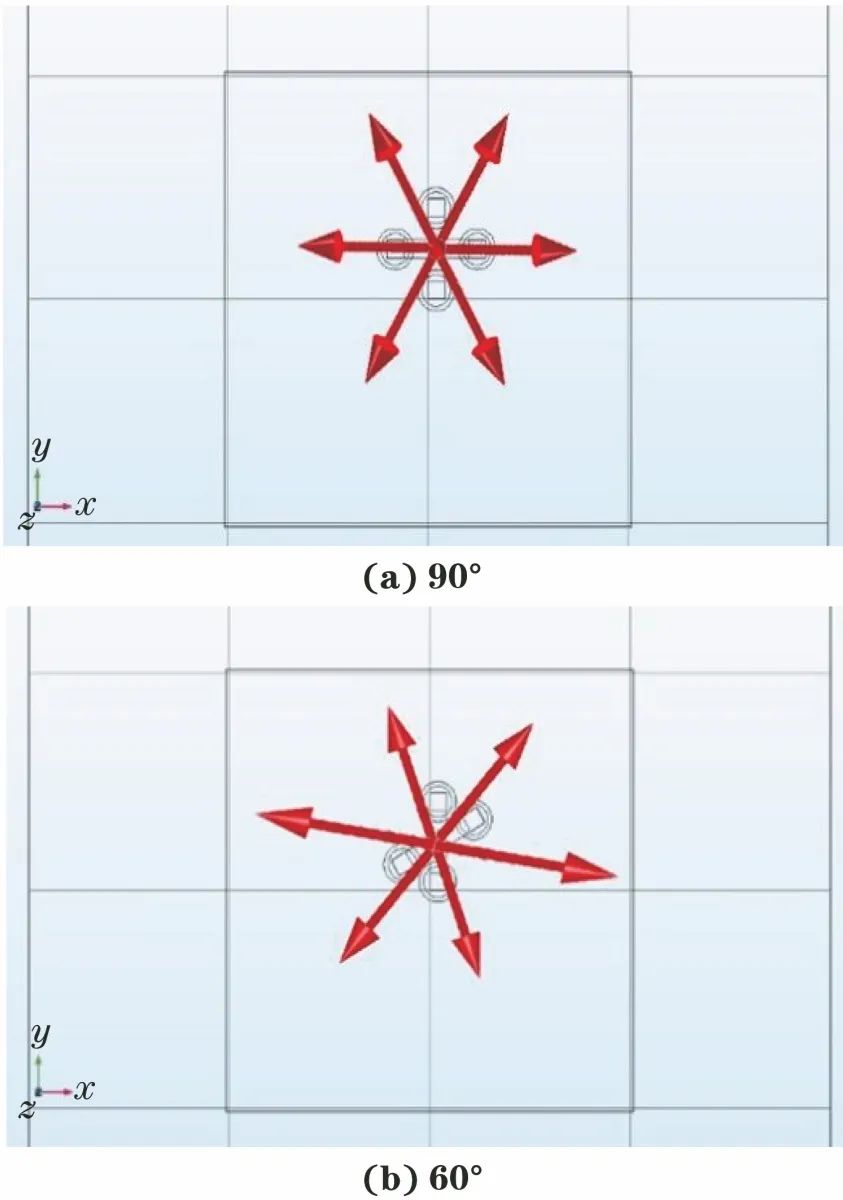
同时计算P点处强度H的变化。由图3可得,磁场强度H峰值下降,整体有效值也随之下降,最大下降幅度25%。
图3 θ减小φ不变时,P点磁场强度H的变化
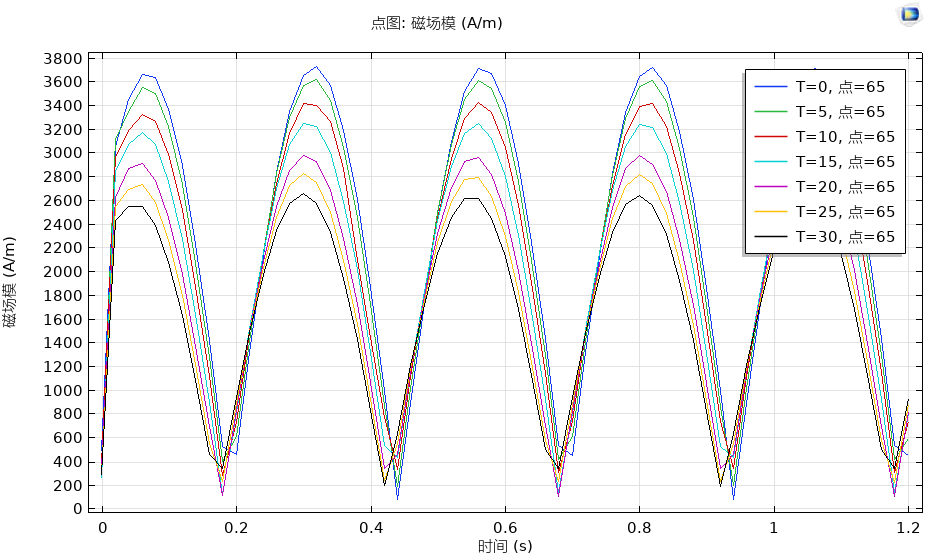
在磁轭上选取M,N两点,分别距P点30 mm(图4),θ减小,保证θ+φ=180°时,计算并对比三点磁场强度H。由图5可得,P点外,交叉磁轭形成的旋转磁场轨迹及变化规律差异较大,θ=90°时,MN点磁场强度接近相等,但较P点提高10%;θ=60°,M,N相较P点磁场强度分别提高20%、25%。
图4 M、N、P点位置图
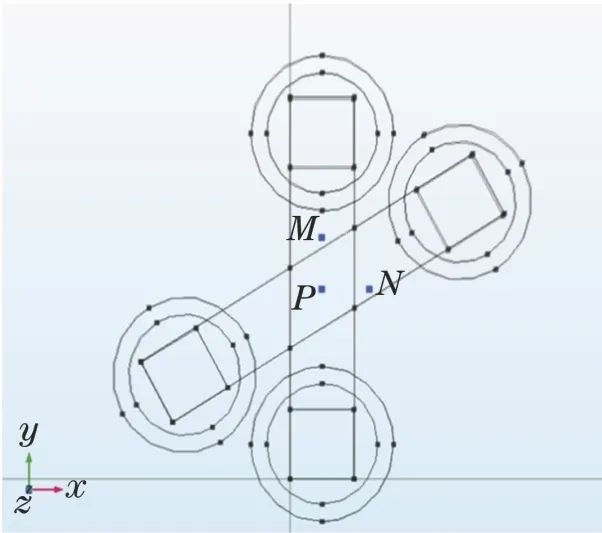
图5 M、N、P点磁场强度对比
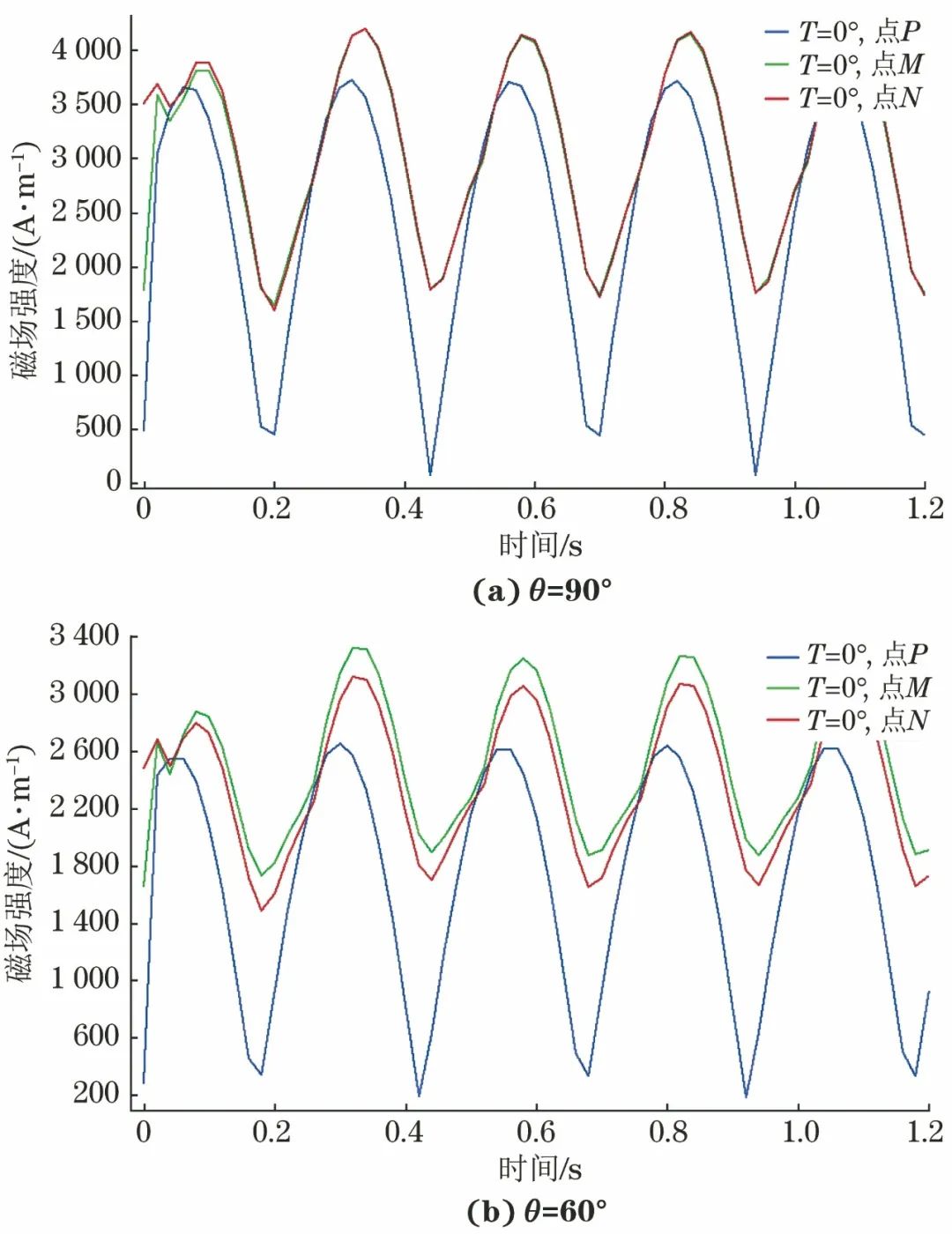
磁轭夹角θ逐渐减小时,调整磁轭夹角电流相位差,保持θ+φ=180°,P点磁场保持圆形,进行参数化扫描,获得中心点P处磁场强度H的变化。由图6可得,磁场强度H变化率不超过3%。
图6 θ减小,保证θ+φ=180°时,P点磁场强度H的变化
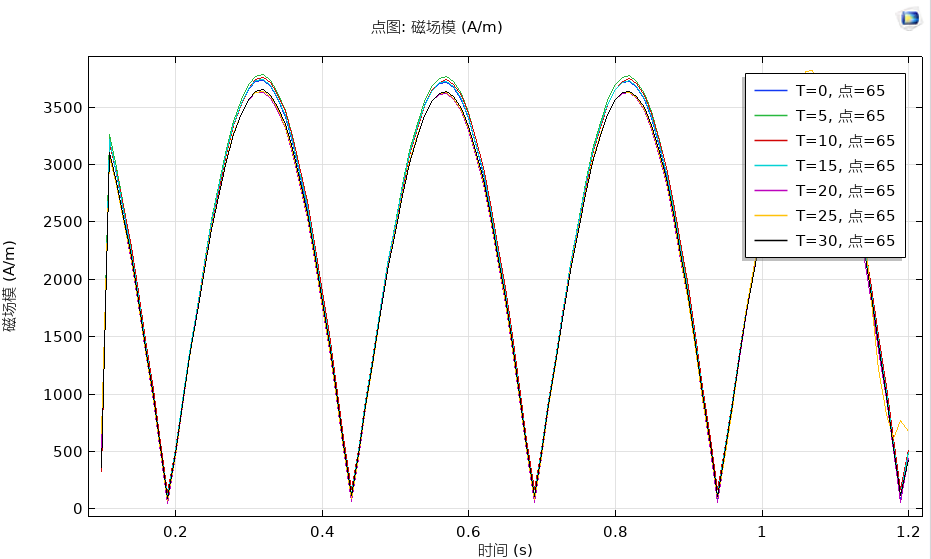
仿真证实,交叉磁轭所形成旋转磁场会随磁轭夹角变化而变化,中心点P磁场轨迹由圆变为椭圆,磁场强度H也随之降低,旋转磁场中各点磁场强度及轨迹不一致。采用相位补偿,可以保证P点磁场强度H基本保持不变。
03
探伤仪性能试验
采用济宁鲁科检测器材有限公司研发生产的旋转磁场探伤仪,根据上文中的研究结果进行相位补偿,磁极间距100 mm,可活动距离最大为16 mm。分别制作DN100/125/150/200的碳钢管作为试验试块,验证仪器提升力、有效磁化范围以及自然缺陷检测能力。
制作不同管径的碳钢管,并在其中灌入金属铅,取G=9.8 N/kg,使每个试块质量为12.04 kg,即118 N,试块规格如表1。
表1 提升力试块规格

提升力测试
将探伤仪放置于不同管径工件之上,同时调整磁轭之间角度,使仪器与工件紧密贴合。在工件上放置砝码,直至工件脱离探伤仪,获得不同角度下仪器提升力。结果如表2所示,因仪器采用相位变化补偿磁轭夹角变化,故仪器提升力最大下降程度约为3%。
表2 提升力试验结果

有效磁化范围测试
将探伤仪放置于不同管径工件之上,同时调整磁轭之间角度,使仪器与工件紧密贴合。将未分割的A1 15/100的灵敏度试片粘贴于工件上,如图7所示。
图7 有效磁化范围试验图
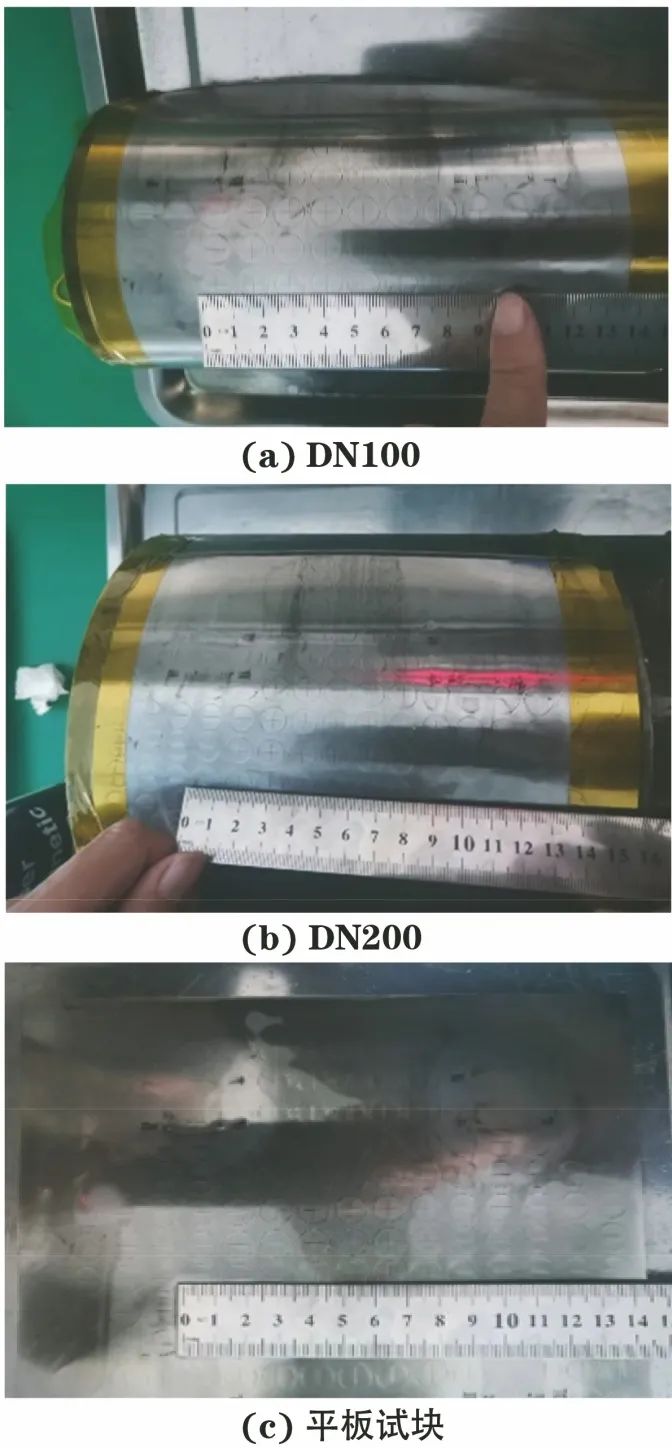
启动探伤仪并进行磁化探伤,测量完整显示出缺陷的灵敏度试片之间距离,获得不同角度下仪器有效磁化范围。结果如表3所示,有效磁化范围相对于平板状态,最大下降程度约为7%。
表3 有效磁化范围试验结果(mm)
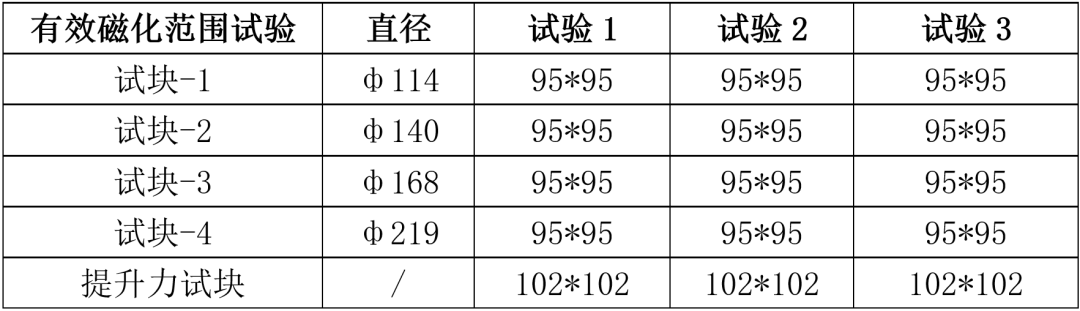
缺陷检验能力测试
选用DN100*6,DN200*10的钢管,试块长度300 mm,在试块周向0°及180°位置加工刻槽,刻槽宽度分别为0.1 mm、1 mm,分别模拟裂纹及条孔缺陷。
如图8所示,刻槽延伸方向为试块轴向,长度150 mm,高度方向自试块内表面向外表面。DN100试块,刻槽深度从3 mm变化至6 mm;DN200试块,刻槽深度从7 mm变化至10 mm,埋藏缺陷最大深度3 mm。
图8 人工缺陷试块图纸

将探伤仪放置于工件缺陷处,调整磁轭之间角度,使仪器与工件紧密贴合,进行磁粉检测,记录试块上显示的缺陷长度,计算获得缺陷的埋藏深度h,如表4所示,磁轭夹角θ=60°时相较θ=90°时,检测深度降低约2%。
表4 人工缺陷检测结果
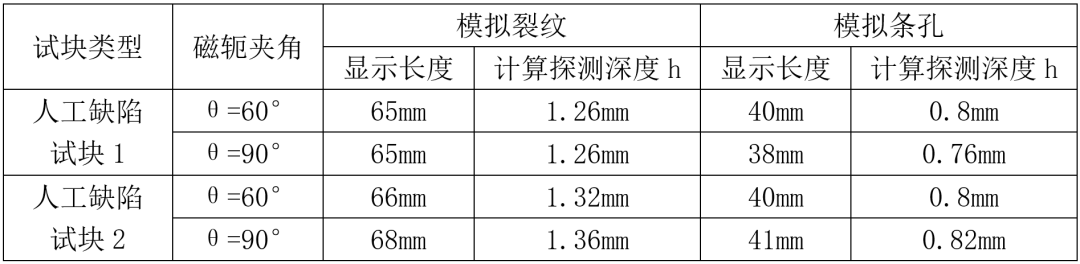
自然缺陷检验能力测试
选用DN100/125/150/200的碳钢管,在钢管上制作对接焊缝并制造自然缺陷,如图9所示。
图9 自然缺陷试块图纸

将探伤仪放置于工件上,调整磁轭角度并进行磁粉检测,检测结果见表5,不低于9 mm长度的自然缺陷均可以做到100%检出。
表5 自然缺陷检测结果
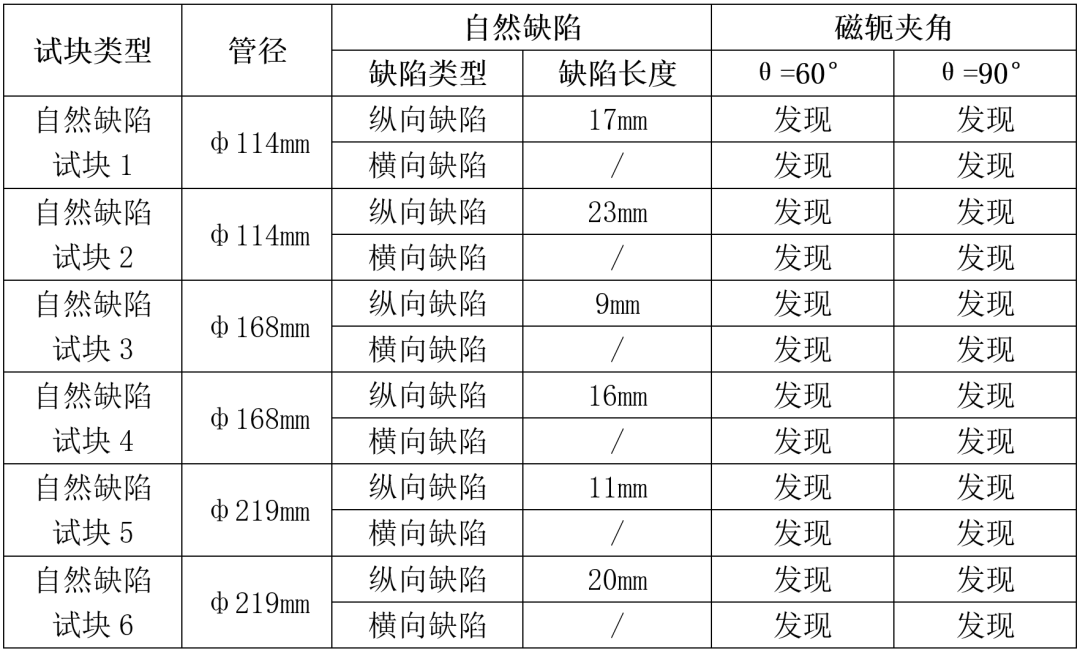
结语
1
旋转磁场的轨迹由磁场强度Hm,两磁场间夹角θ以及两磁场间的相位差φ共同决定,θ+φ=180°时,P点磁场轨迹为圆形,其他时刻为椭圆形,除P点外,各处磁场分布不均匀,变化规律也不相同;
2
在磁轭夹角θ增大,φ不变时,P点磁场强度H逐渐降低;θ增大,保证θ+φ=180°时,P点磁场强度H基本保持不变;
3
将旋转磁场探伤仪底部关节活动距离转化为磁轭夹角θ的变化,通过调节电流相位差φ,可以保证探伤仪的提升力、有效磁化范围及缺陷检出灵敏度不低于常规磁粉探伤仪。
来源:济宁鲁科检测器材有限公司
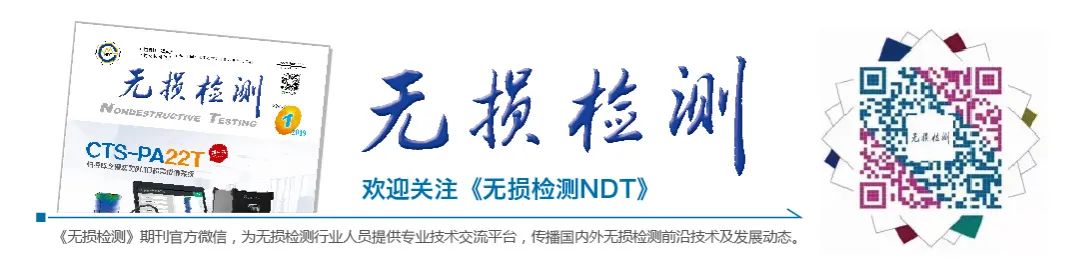
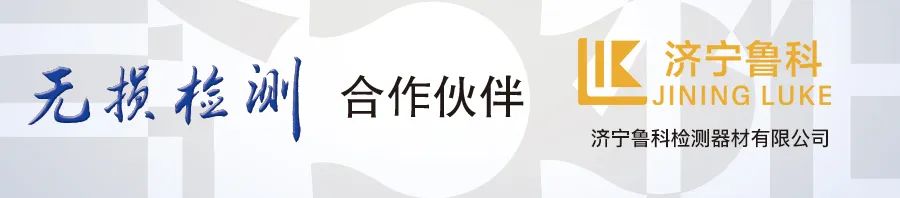
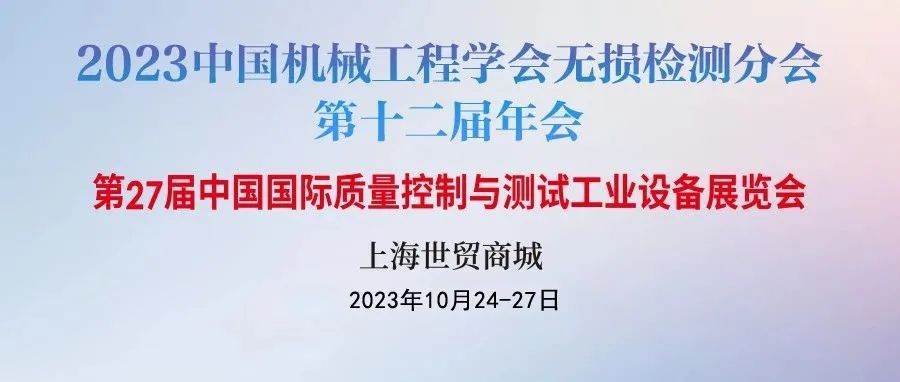
致力成为国内一流的海洋与能源工程综合业务供应商